Galvanized has become increasingly popular in the automotive manufacturing space as a corrosion resistant coating on steels. Mainly, it's put on there in a hot dip fashion where you're actually dipping the material in molten zinc and coating it that way. There's electro plating and galvanneal plating also.
The most that I dealt with in the field was hot dip. It's by far less expensive to do it this way and the coating seemed to stand up a little bit better just because of the thicker weight of the coating.
Many automotive manufacturers will be going to hot dipped galvanized today because they’re running thinner materials. You're seeing it more in welding because of the lightweighting that OEM automakers are doing. Tier 1 suppliers are now needing to accommodate this as well into their welding process.
Galvanized Welding Challenges
So what makes this a challenge when it comes to robotic welding? The biggest obstacle is that galvanized material doesn't melt and mesh well with molten welding material.
Zinc has a much lower melting temperature than steel does, and then by the time you get your steel heated up to be able to melt together, you're vaporizing the zinc because it has such a much lower melting temperature than the steel does. You're actually burning it and creating a gas.
That makes the first biggest issue with galvanized welding porosity. You have this out-gassing of zinc material from the surface of the steel and then that out-gassing can either:
- Get trapped inside your molten weld puddle, and create internal porosity
- Get to the point where it's escaping and create visual porosity in the weld
Excessive Spatter
The other huge issue with galvanized steel welding is the spatter. With the out-gassing, when this boils off, it's actually creating a disturbance in your weld puddle as the zinc boils off the material and creates more spatter because you're disturbing the weld puddle. You're having these gas bubbles burst in your weld puddle, which sends molten metal flying all over the place.
This excessive type of spattering creates a maintenance nightmare on your tooling with the spatter and with the powdered zinc. It cakes itself onto anything everywhere and creates a really fine particulate that settles in everywhere. Can really hurt your tooling by building up on rust blocks, which then creates dimensional issues when you're putting parts together.
Zinc spatter build up also causes collision errors with welding torches because of the spatter and dust built up on the tooling.
Fume Extraction Galvanized Welding
Number three is an environmental concern about it. Galvanized weld fumes are toxic to breathe in, so it creates a much higher need for proper ventilation. Capturing your zinc fumes before they can get to your operators or your welders is a big deal and it's being taken a lot more seriously now.
The density of smoke emitted from galvanized welding creates a huge fume extraction need. Underestimating this can become a huge creep on your time and budget for industrial equipment.
When we first purchased fume extraction equipment to control weld fumes from our galvanized process it was said that under normal conditions these filters have to be cleaned once or twice a year.
Filters ended up needing to be cleaned three times a quarter. This meant the entire shop would need to temporarily halt production in order for a change out of the extraction filters. Doing a cleaning or replacement of that magnitude can reach up to $100,000 if the equipment need is that high.
That ended up being a large but necessary cost burden because we underestimated the fume extraction needs for galvanized materials. You also have to be careful with how you dispose of it, because you can't just pull it out and trash it. It has to be disposed of properly. You usually need to have an industrial safety crew that understands the environmental impact and can dispose of it properly.
Welding Wire Types for Galvanized Steel
Galvanized steel welding approaches vary significantly depending on your choice of filler metal. Whether you opt for a solid core wire or a metal core wire, you’ll have different challenges you’ll have to pay attention to in order to weld successfully without constant maintenance needs.
Solid Core Wire
With solid wire, you're still able to get a good weld. But, you will end up with massive amounts of spatter. The best way to combat that kind of spatter buildup is slowing down your travel speed.
What this does is it allows the material to heat up before the puddle helps vaporize the zinc coating before the welder gets to it. Also, when you're moving a little slower, it allows your welding puddle to cool slower as well. And so you get a better possibility of outgassing of this zinc through your molten weld instead of it getting frozen into it.
For the spattering issues, you can mess around with parameters and gas coverage and things like that, but to be perfectly honest with you, it's going to be an ongoing issue.
There hasn't been a good solution found to eliminate spatter often on galvanized material with a solid core wire. Mostly just finding ways to cover surfaces that are going to be an issue for spatter or mating surfaces, bolting surfaces, things like that.
Covering those sources as essential. We always used a brass or a copper covering, or something on an air cylinder depending on how advanced your tooling is, or even put it on a swing, cover up your part, cover your threads. Make sure you're covered for spatter on the tooling as much as you can.
Another huge issue when you weld galvanized with solid wire is encountering porosity at the surface. We did a ton of testing on galvanized using solid wire on truck frames that we were welding, and we found that we were able to get beautiful looking welds with a solid wire.
What we didn’t see until we x-rayed them was a prevalence of internal porosity in the weld. Even in regular cut sections it was spaced out enough that you'd have a really hard time running into it when you do a cut niche.
Metal Core Wire
For metal core wire, what we found at Tower was that the best solution utilized a tubular wire filled with powdered metal and flux and cleaning agents and things like that. Those additional agents within the wire allowed the puddle to stay molten longer and allowed for outgassing like with the solid wire. But, you're able to move at higher travel speeds because of the puddles staying molten longer.
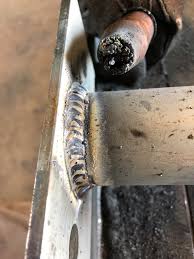
Like with solid core, you’re able to use the same type of gas or 90/10 mix, argon, CO2. But what we found is you have to weld in a flat position and you couldn't really run any straight downhill welds with this type of filler. What ended up happening is you ended up defeating the whole purpose of the wire.
Since the puddle would solidify faster because it's running faster you would get overlap with that weld puddle because it's rolled so quickly. It was easy for it to get ahead of the arc. You ended up with a cold lap, thus not allowing the zinc to melt off before it gets there so it gets trapped under that puddle to create internal porosity. And a lot of times external porosity as well.
So in order to use a metal core wire we had to utilize positioners that put everything in a flat position to allow for a lot of that gas to escape. Out-of-position robotic welding is not something I would recommend for metal cored wires when welding on zinc.
Flux Core Wire
You can go to a flux-cored wire as well for robotic welding galvanized steel, which can be shielded by gas or can be self shielded. Flux core does well at pulling the impurities, in this case the zinc, out of the molten puddle, leaving it on top. But this usually doesn't work for automotive robotic welding because you need to put in a post cleaning process for it. It leaves a slag on top of the weld which can flake off after painting and things like that. Many au
tomotive OEMs don't like using that.
Another big issue is a weld finish on there too. It looks very different across each wire type. Even from solid wire to metal cored and flux cored, your weld looks very different than if you just welding regular uncoated steel. The weld is very matte in color or in finish. It's not very shiny and looks very gray and kind of dull and dirty.
Weld Silica from Galvanized Material
Also, from this zinc being pulled out and bubbling up to the top, the cleaning agents in any of these wires, silica to be exact, is usually an issue. You end up with silica islands on your welds, which are just little puddles of brown glass that ended up on top of your weld. These cause issues.
First, and we ran into this issue a lot in my time working for Tier 1 suppliers, is that end-users would think that they had rusty welds on their vehicles because the coat. Silica causes the paint that you use to paint the frame to not stick to the glass because you use an electrical coating process and silica acts as an insulator. This means you're not able to electric coat very well or you can't electric coat that material at all.
How Much Maintenance is Needed for Galvanized Welding?
Maintenance needs on galvanized welding operations is a huge commitment. You're having to clean parts, clean finished parts, perform a post-cleaning cleaning, perform sanding, grinding, and then chipping away any spatter if it's not covered properly.
A lot of weld finishing is grinding out porosity or some spatter, those kinds of things. But with galvanized welding for the maintenance side of things, your actual tooling also builds spatter up very quickly.
Zinc spatter is very sticky and sticks right to your tools if you're not in there cleaning it twice a shift depending on your volume. You likewise have to make sure the floors are swept inside because it piles up on the floors and the tooling; you have to go in with a hammer and a chisel.
At Tower, we tried a lot of different paints and coatings to put on the tooling and found some things that helped some spatter protectors, some paint-on spatter shield, things like that. But the most helpful was when we were able to get in there about twice a shift and go in and clean up tools.
Also with that maintenance wise, if you are running a metal-cored wire to run faster travel speeds and to get more of that porosity out of your weld puddle, another big issue is a metal-cored wire is nowhere near as smooth as the copper coated solid wires. This means you end up wearing out drive rollers faster as well as wire liners and especially tips. These consumables become worn more from the roughness of the wire and how much of it you're feeding out.
Being prepared for that increased maintenance needs is important. Galvanized steel welding will definitely lead to more frequent consumable changes, very frequent shell cleanings, and an increase in tool cleanings to be able to get spatter and debris off your tooling. This all means more heads on the floor and the maintenance department to be able to handle the demands of galvanized welding.
Summary
Galvanized steel is not an easy material to weld. But with it's increased need in the Automotive OEM world - and likely beyond, it's use is going to continue to rise.
The more you can plan ahead and be aware of the steps necessary to weld galvanized material, the better you will be able to account for both budget and manpower needs to keep a smooth production line going.