Are you considering investing in a seam tracking sensor for automated welding, but are unsure where to begin? You're in the right place! This blog provides a comprehensive starting point for understanding what makes an excellent seam tracking sensor and when to invest. To achieve flawless welds, robots need precise guidance, which is where seam tracking sensors come in. In this blog, we'll explore the essential properties of top-notch seam tracking sensors.
Key Sensor Properties Covered:
- Precision
- Reliability
- Flexibility
- Ease of Use
1. The Power of Precision in Seam Tracking Sensors
2. Reliability: Consistency in Demanding Environments
/News%20Abo%20Mailing/2024_welding_tolerances_210x240px.jpg?width=210&height=240&name=2024_welding_tolerances_210x240px.jpg)
Look for features like:
- Gas and liquid cooling systems for optimal temperature regulation
- Optional cooling elements to lower air temperature
These technologies ensure consistent accuracy and minimize downtime, even in the most demanding welding environments.
3. Flexibility: Adapting to Diverse Applications
A top-notch seam tracking sensor offers versatility, catering to various welding applications. This flexibility is particularly beneficial for system integrators, eliminating the need to master multiple sensor technologies. With a single, reliable sensor, you can:
- Streamline system integration
- Accommodate diverse customer needs
- Address special applications without requiring specialized systems
This adaptability enables efficient customization, reducing the necessity for application-specific sensors and minimizing complexity.
4. Ease of Use: Streamlining Operations
Key features include: -4.png?width=247&height=247&name=Untitled%20design%20(3)-4.png)
- Intuitive guidance for effortless operation
- Selective information display for task-specific needs
- Minimal training requirements
This ease of use, combined with flexibility, allows:
- Seamless adaptation to diverse applications
- Efficient welding cell repurposing
- Quick adjustments for new components
When to Invest in a Seam Tracking Sensor?
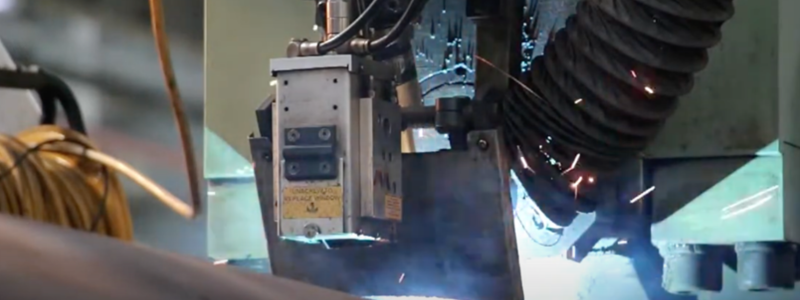
Seam tracking sensors yield significant advantages:
- Increased production efficiency through minimized rework and rejects
- Lower running costs and lighter components via reduced material and shielding gas consumption
- Enhanced safety and environmental friendliness
- Faster welding with high-quality results
Wrap up
Need assistance? We're happy to help. ⬇️
Want to learn more?
Check out some of our other content ↓