Electric cars, hybrid vehicles, modern transport systems for freight traffic – the future belongs to electromobility. More product functions mean more electronics, which in turn mean more weight for the designs. On the other hand, there are the legal regulations for reducing emissions, which can often only be complied with or fulfilled by reducing weight. One solution is the use of lightweight materials for constructions of modern transport systems, such as aluminum. But aluminum tends to be a bit of a "diva". You need very specific prerequisites and welding equipment to weld aluminum alloys properly. Process reliability is a top priority in aluminum processing.
Prof. Emil Schubert
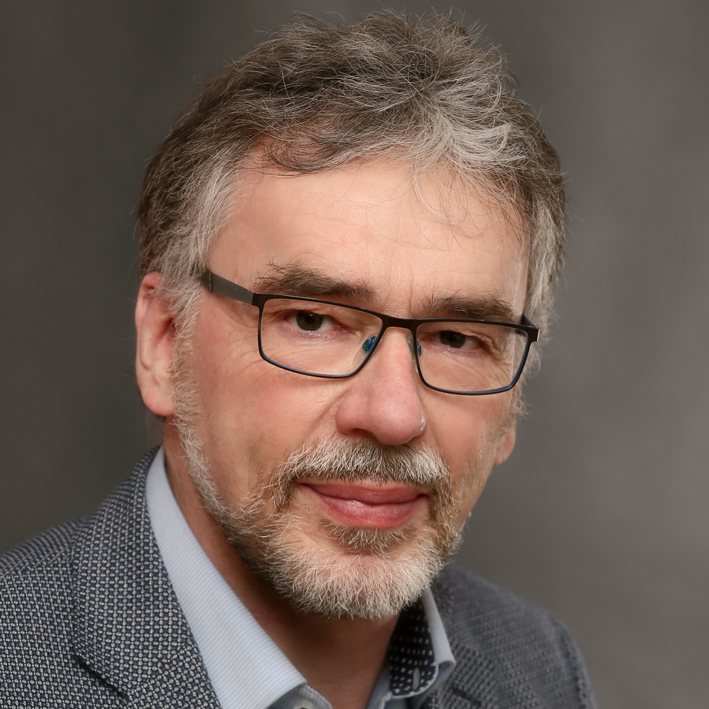
Recent Posts
Welding procedures in aluminum processing
Topics: Aluminum Welding
Save up to 50 % gas during gas-shielded welding
Horrendous electricity and gas bills, increasingly expensive food, unaffordable repair services ... the current situation is the number one topic of conversation with neighbours and in the media. As citizens, you save wherever you can and do without many things that used to be a matter of course. In industry, people are constantly looking for cost-cutting measures that must not, however, restrict production. Welding companies and other manufacturing companies that employ skilled welders are not exempt from this. Where can savings be made in welding if the quality of the products must not suffer under any circumstances? There is one approach that is often not recognised as a savings potential: shielding gas.
Topics: Gas Management
Pickling metal – which treatment is best?
Beautifully crafted railings and staircases made of stainless steel, high-gloss kitchen fronts or building facades that gleam in the sun from afar are already real eye-catchers. To turn a metal into an end product worth looking at, the surface must be treated accordingly. In metalworking, pickling is used in addition to grinding, brushing or blasting. There are different approaches to this, depending on the requirements in the production process.
Topics: Welding Chemicals
Optimising the service life of welding robots
In the two previous blogs on how to reduce downtime with welding robots, the focus was on the robot torch and its wear parts.
Topics: Robotic Welding
Downtimes due to wear parts during robot welding
In our first blog on how to reduce downtimes with robotic welding equipment, the focus was on robotic torches. We looked at the right choice of robot welding torch, torch power, torch geometry and highlighted that without “clean”' programming none of this will work.
Topics: Robotic Welding
How to avoid or reduce downtimes with welding robots
When it comes to high quantities, cost and time pressure, welding robots provide valuable assistance. With them, consistent quality can be achieved in the shortest possible time. However, productivity in automation or robotics also depends significantly on how often and how long a welding robot is at a standstill because it has to be reloaded, set up again after a crash or generally maintained. Every second of downtime counts and costs money. And it cannot be generalised who is more affected by downtimes in production: the group with large robot production lines or the small medium-sized company that only has one welding robot in operation. A welding robot in industry must function trouble-free as much as possible – and having the right equipment in production or in the company helps with this. Find out here how to reduce downtimes for welding robots.
Topics: Robotic Welding
Which are the best gas nozzles for MAG welding?
Practical tips about all you need to know about gas nozzles for MIG/MAG torches
The MIG/MAG welding process is very demanding and both man and material are pushed to their limits? – often even beyond. Therefore, it is all the more important to work with good tools, especially the welding torch with its wear parts. These parts are very close to the process and have to withstand heat and weld spatter for as long as possible. Especially the gas nozzle, which, in addition to its actual task, is often misused as a hammer.
Topics: MIG/MAG
Cause of weld spatter: GMAW welding and electric arc
Gas-shielded metal arc welding – also known as GMAW welding or MIG/MAG welding – is by far the most applied and most common welding process in welding technology. When searching for the cause of weld spatter, this process literally hits the bull's eye. Whereas with TIG welding and plasma welding almost no weld spatter occurs, spatter formation in GMAW welding can never be completely prevented. The question may arise why not use TIG or plasma welding in general if welding spatter should be avoided as much as possible. To get the answer it is necessary to take a closer look at the process of MIG/MAG welding and the cause of weld spatter.
Topics: Welding Chemicals
How Gas Management Will Change for the Internet of Things
If a technically interested person opens a magazine or a newspaper you cannot avoid reading articles about how the “Internet of Things” will change our daily live in the coming years.
Topics: Shielding Gas